- Ford has teamed up with McDonald’s to turn waste coffee chaff into biohybrid plastic car parts.
- Manufacturers have many kinds of sustainable trim materials, but a coffee plastic headlamp housing is the first “real” car part made with these materials.
- The coffee plastic is also lighter than traditional plastic and requires less energy to make.
Ford and Ferrari were racing rivals once upon a time, but today, the Italians might appreciate emerging coffee technology. CNET reports that Ford and McDonald’s have combined their efforts in order to make car parts using recycled coffee chaff. By combining recycling with coffee, Ford’s stock as the official brand of dads continues to rise.
When coffee roasters put beans through a roaster, a papery skin called chaff comes off which, CNET reports, “tends to get into everything and there's lots of it.” It’s similar to the stuff on peanuts and also the trope-namer for separating the wheat from the chaff. Farmers let wheat chaff literally float away on the wind. This is less feasible inside a coffee roaster.
Engineers have combined specially treated coffee chaff and plastic to form hybrid pellets that can be used in place of traditional petroleum plastic in some car parts. The chaff-plastic can be melted and molded, and it’s lighter and less energy-intensive than full petroleum plastic. Ford is quick to point out this isn’t its first foray into biohybrid materials, because the automaker has used a soy-hybrid foam in many car seats beginning in 2007. The American soybean lobby has incentivized Ford’s investigation of soy in rubber and other applications as well.
Plastic-like replacements made from plants aren’t the newest technology; corn packing peanuts, which are basically just Cheetos puffs without the cheese dust, have been around for decades. These products are old enough now that there are think pieces suggesting they’re not good enough anymore. But Ford’s applications, first with soy foam and now with coffee plastic, represent a move to rely on biohybrid materials for permanent, durable applications. They’re not cushioning your breakables for a one-way trip or providing disposable cutlery.
Ford’s flagship part for its new coffee plastic is headlamp housing. Ford told CNET the coffee plastic is really good in high heat, and anyone who’s changed a headlamp knows it’s a surprisingly heavy part; the coffee plastic weighs 20 percent less than the equivalent traditional plastic. Reducing weight is vital not just to racing cars, but to consumer cars as well because of the link between weight and fuel consumption. Shedding weight in non-structural parts of the car is the easiest way.
CNET expresses hope that Ford will license its coffee plastic to other manufacturers, but precedent isn’t on its side. Ford’s soy foam has stayed in just its vehicles, although it’s not clear if that’s because of proprietary technology, or that no one else was interested in this specific tech. Other manufacturers have their own versions of biohybrid materials, using everything from sugar cane to recycled jeans.
But again, these are almost all trims and liners, not actual parts. A promising heat-tolerant and manufacturable bioplastic may be a gamechanger, or at least a sign that similar developments will follow from other manufacturers. In the meantime, the other major use of coffee chaff is still to be processed and pressed into charcoal briquettes, which rely on fillers like chaff or wood dust.
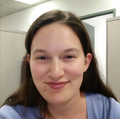
Caroline Delbert is a writer, avid reader, and contributing editor at Pop Mech. She's also an enthusiast of just about everything. Her favorite topics include nuclear energy, cosmology, math of everyday things, and the philosophy of it all.